Tratamento de recursos de augas residuais de biofermentación mediante secado por pulverización
A produción limpa, a vertedura cero de augas residuais industriais e o logro dun fermoso ambiente ecolóxico sempre foron obxectivos perseguidos polas persoas, pero na produción industrial real non é doado de conseguir, especialmente as augas residuais de alta concentración, que necesitan ser diluídas, filtradas, neutralizadas e oxidadas e os métodos de tratamento bioquímico, para tratar as augas residuais en auga cualificada de segunda e terceira clase. Os métodos tradicionais de tratamento de augas residuais aumentaron os custos operativos das empresas, facendo imposible que as empresas garantan o tratamento consciente das augas residuais industriais; con todo, o equipo de secado por pulverización producido pola nosa empresa pode resolver este problema.
As augas residuais tamén son un recurso. Na industria bioquímica, na industria química dos sales inorgánicos, na industria alimentaria, na de procesamento da carne, na industria do papel, no alcohol e noutras augas residuais industriais que conteñen celulosa, azucre, proteínas, ácidos nitroxenados, sales inorgánicos e outros recursos útiles, tirar é prexudicial, sacar é un tesouro. O tratamento das augas residuais extrae recursos útiles mediante evaporación e condensación de vapor, non é auga residual. Para lograr unha produción limpa e un ambiente verdadeiramente fermoso.
Algunhas substancias útiles, como as proteínas das augas residuais, pódense converter en condensado de vapor mediante unha ou máis etapas de separación e secado por pulverización, e as substancias útiles das augas residuais pódense converter en aditivos para a alimentación, como a carne. A auga do sangue e a auga de lavado da carne na planta de procesamento combinado tirábanse como augas residuais no pasado, o que contaminaba o medio ambiente e perdía recursos. Os países estranxeiros utilizaron este proceso para recuperar todas as proteínas do sangue e vendelas ás plantas de alimentación. A planta combinada obtivo beneficios económicos, matando dous paxaros dun tiro. Na industria do amidón, o millo, o trigo, as patacas, etc., a auga de lavado e a auga de remollo conteñen amidón, proteínas, ácido láctico e similares. Moitas fábricas de amidón nacionais descartárono como augas residuais, que se poden evaporar e concentrar ao 50 % e logo secar por pulverización en aditivos para a alimentación de proteínas, mentres que a auga de remollo convértese en condensado de vapor, que se pode reciclar como auga de proceso. O ambiente podre da fábrica de amidón desapareceu para sempre e, ao mesmo tempo, produce beneficios económicos.
As tecnoloxías mencionadas anteriormente son procesos físicos sen reaccións químicas e son tecnicamente maduras e fiables. Cando o pobo chinés domina estas tecnoloxías, hai novos desenvolvementos e innovacións, pero para completar un deseño de enxeñaría, débese calcular o equilibrio de materiais e calor. Isto require a cooperación das empresas para proporcionar os parámetros físicos e químicos básicos da auga residual.
Clasificación das augas residuais procedentes da produción de licor de biofermentación e aplicación do secado por pulverización
Augas residuais de glutamato monosódico | |
Líquido concentrado de cola disxuntiva | Fertilizante composto |
Polpa de millo | Aditivo proteico para pensos |
Augas residuais biofarmacéuticas | |
Augas residuais con vitamina B2 | Aditivo para a alimentación |
Augas residuais de cefalosporinas | Aditivos para pensos |
Augas residuais de lévedo | Os aditivos proteicos para pensos, ao mesmo tempo, poden ser procesados adicionalmente en péptidos proteicos de lévedo |
Augas residuais de alcohol | Fertilizante orgánico composto |
Augas residuais de heparina sódica | Aditivos proteicos para pensos, que poden ser ademais |
Augas residuais de condroitina | Aditivos proteicos para pensos, que poden ser ademais |
1. Material: axeitado para varios materiais
2. Temperatura de entrada de aire: 120 ℃ ~ 700 ℃
3. Temperatura de saída de aire: 60 ℃ ~ 400 ℃
4. Produción de po seco: 50 kg/h ~ 4000 kg/h
5. Contido sólido: 5% ~ 55%
6. Fonte de calor: calefacción eléctrica, vapor acendido, forno de combustión de gas natural, forno de combustión diésel, vapor sobrequentado, forno de combustión de biopartículas, forno de carbón, etc. (pódese substituír segundo as condicións do cliente)
7. Modo de atomización: atomizador centrífugo de alta velocidade, pistola pulverizadora a presión
8. Recuperación de materiais:
a. Eliminación primaria de po por ciclón (recuperación do 97 %)
b. Desempolvación primaria por ciclón, desempolvación por película de auga (recuperación do 97 %, 0 descargas)
c. Desempolvación primaria mediante ciclón máis desempolvación de bolsas (recuperación do 99,8 %, 0 descargas)
d. Eliminación de po de bolsas en dúas etapas (recuperación do 99,9 %, 0 descargas)
9. Control eléctrico: (control automático da temperatura de entrada de aire, control automático da temperatura de saída de aire, temperatura do aceite do atomizador, alarma de presión de aceite, visualización de presión negativa na torre)
a. Control de programas PLC
b. Control DCS completo do ordenador
c. Control por botón do armario eléctrico
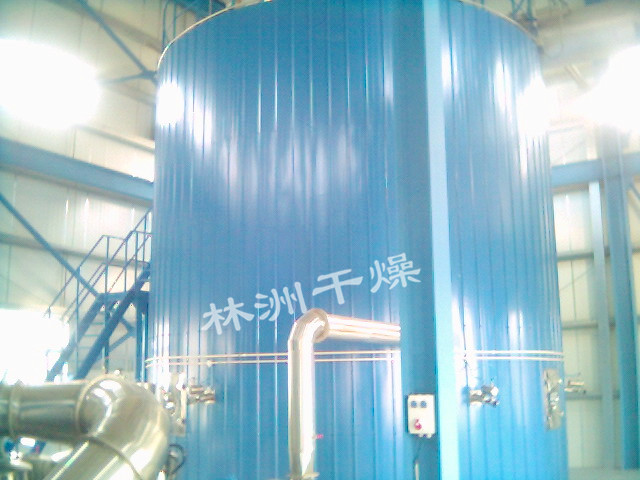
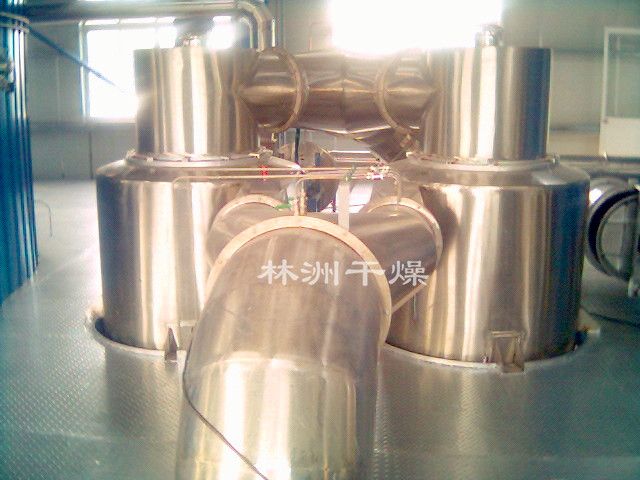
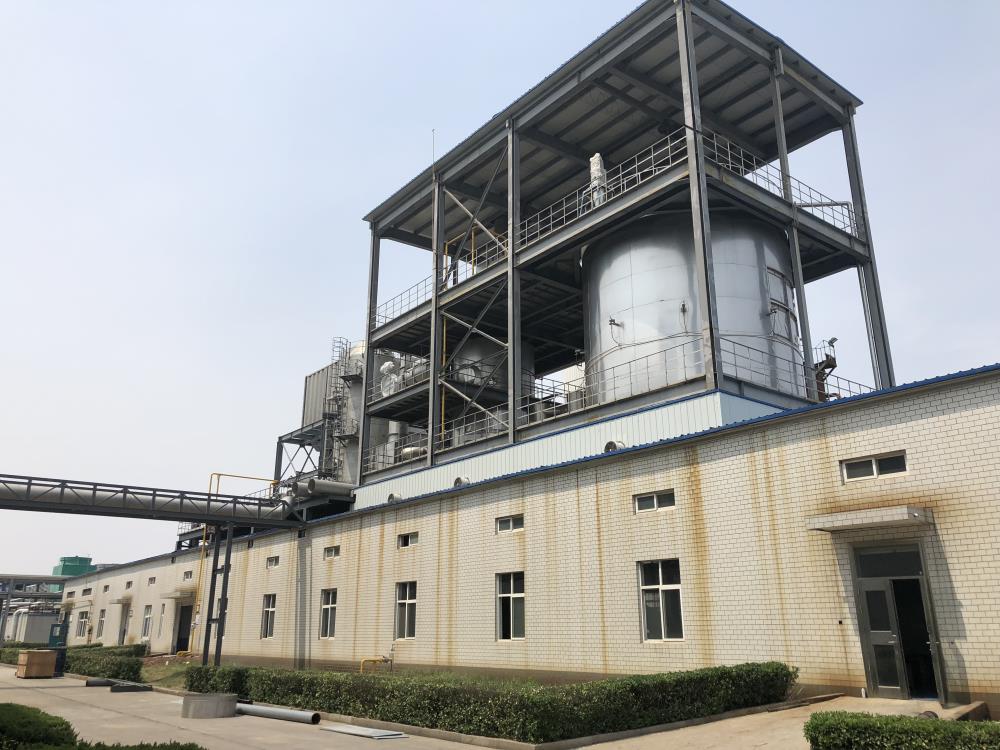
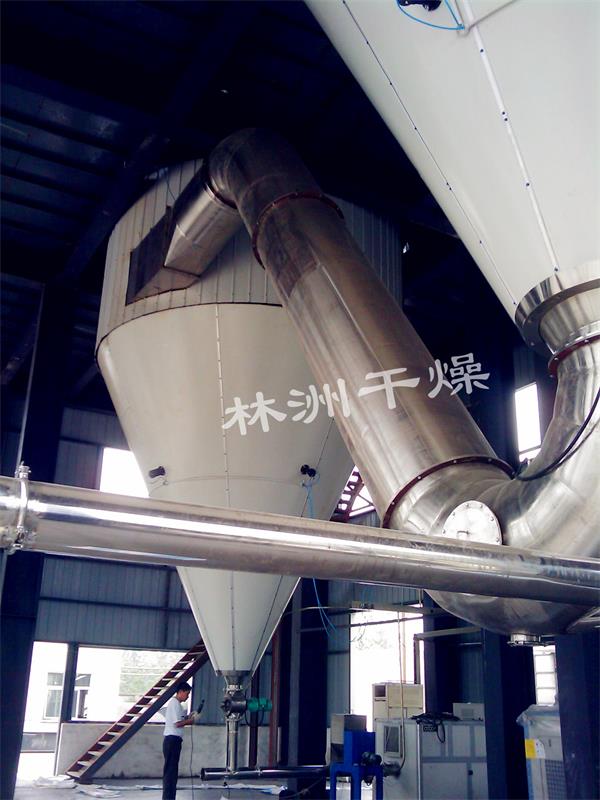